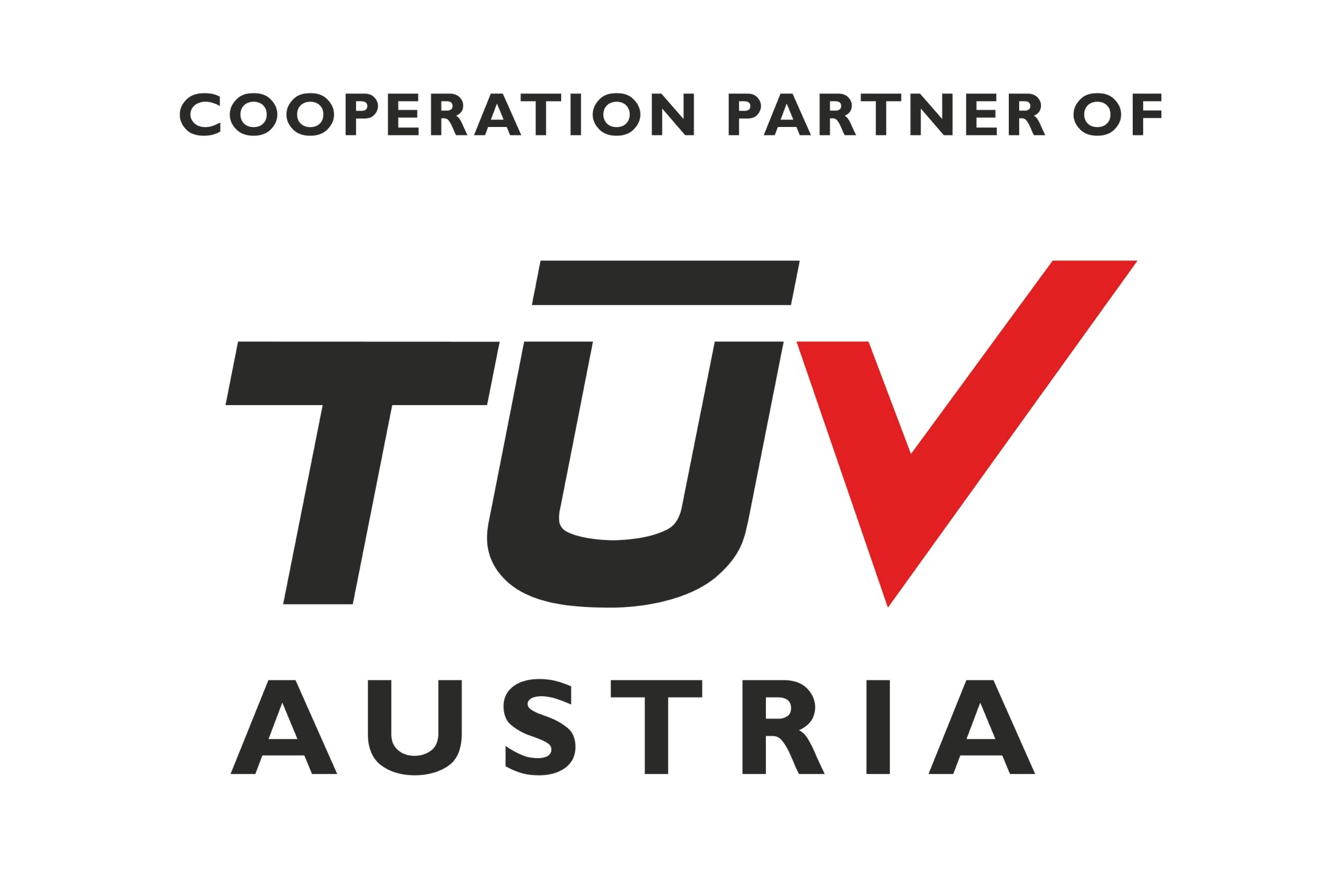
Quality Management
1) CQR: Certified Quality Representative
Duration: 4 Training days + 1 Examination day
Training for certified Quality Representatives
for QM systems according to ISO 9001:2015
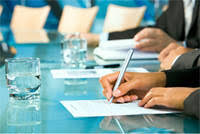
Overview of various processes of quality management and their practical application:
· the updated family of standards of the ISO 9000 series
· basics of integrated management systems and TQM
· structure, supervision and permanent improvement of QMS
· the ISO 9001 process management model
· interpretation of standard requirements
· procedures & tools, internal & external audits.
A personal certificate according to ISO/IEC 17024 issued by TUV AUSTRIA provides you with international recognition of your expert qualifications as a quality.
Course units: 24
2) CQT: Certified Quality Technician
ADVANCED TRAINING
Quality Management Systems Internal Auditor acc. to ISO 9001:2015 (IRCA approved)
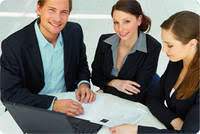
This is an ideal entry level auditing course. A highly interactive and engaging two day event that will help anyone interested in using the internal audit as a tool for continual business process improvement.
It will introduce you to the concepts of auditing for conformance, risk and process effectiveness, and equip you with the skills and techniques to produce incisive, reliable and value adding audit reports.
This course has a strong bias towards process auditing and continual improvement. It is designed for those of you that see auditing as an integral business improvement activity and part of a cohesive overall quality strategy.
Course units: 16
BASIC TRAINING
Basics of quality management technician
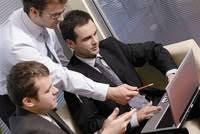
Essential aspects for all employees and executives, as well as a first step in the training of individuals employed in quality management functions; you will be trained in the basic elements of quality management and its success factors.
Course units: 8
Price: on request
Contact: Stefanie Kirchhof, MA, Tel: +43 (0)5 0454-8174, Fax: +43
3) CQM: Certified Quality Manager
BASIC TRAINING
Examination for certified Quality Managers
A personal certificate according to ISO/IEC 17024 issued by TUV AUSTRIA provides you with international recognition of your expert qualifications as a quality manager.
Course units: 8
4) CQA: Certified Quality Auditor
Duration: 4 weeks, each 4 days, each 4 h = 64 h
ADVANCED TRAINING
The updated ISO 19011
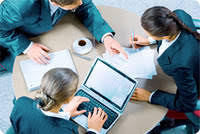
conclusions of the updated version of ISO 19011, as a code of practice for:
· the management of audit programmes
· the performance of audits on all management systems
· enhancing the competence & assessment of auditors and auditor teams
· the development of own audit requirements
Course units: 8
ADVANCED TRAINING
Quality Management Systems Lead Auditor acc. to ISO 9001:2015 (IRCA approved)
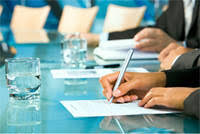
This five day course is for the serious quality management system auditor. A challenging course that will equip you with the planning skills to lead an audit team, carry out complex supplier audits, external 3rd party audits and deliver accurate, defendable and value adding audit reports. This course has a strong process and continual improvement bias, suitable for those of you who are interested in auditing to establish the overall capability of the management system to sustain and improve its performance. The course has been adapted to take into consideration the release of ISO 9001:2015.
Course units: 40
STATISTIC THEORY & QUALITY MANAGEMENT TOOLS TRAINING
Course units: 16
5) OHSM: Occupational Health and Safety Management Systems Internal Auditor – acc. to OHSAS 18001:2007 (IRCA approved)
Duration: 2.5 weeks, each 4 days, each 4 hours
ADVANCED TRAINING
Occupational Health and Safety Management Systems Internal Auditor – acc. to OHSAS 18001:2007 (IRCA approved)
This is an ideal entry level health & safety auditing course. A highly interactive and engaging two day event that will help anyone interested in using the internal audit as a tool to evaluate levels of legal compliance and continual OHS improvement. It will introduce you to the concepts of auditing for compliance and OHS improvement, and equip you with the skills and techniques to produce incisive, reliable and value adding audit reports. It will also introduce you to the OHSAS 18001:2007 model for occupational health & safety management systems.
Course units: 40
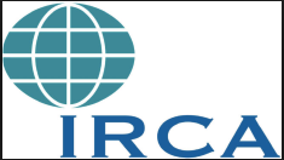